Why Manufacturers Must Transform the Worker Experience to Thrive
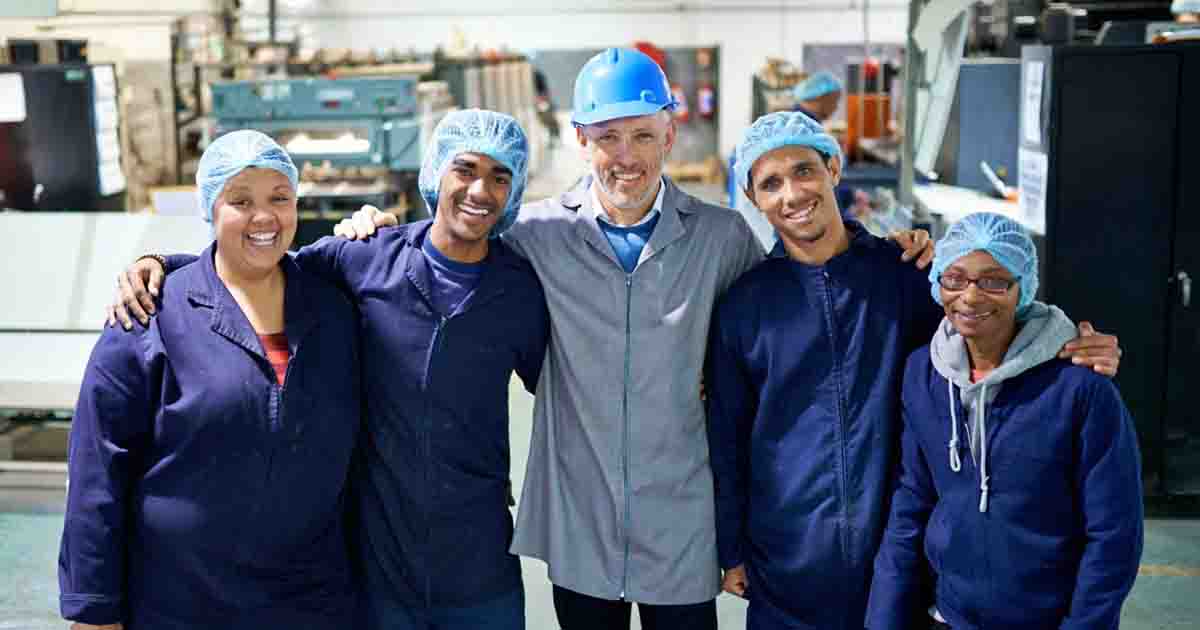
Talent in the manufacturing sector is increasingly scarce. A survey by the British Chambers of Commerce (BCC) reveals that 78% of companies across construction, production, manufacturing, and logistics are struggling with severe recruitment challenges.
In the UK, there are currently 1.3 million job vacancies, with fewer workers available compared to pre-pandemic levels. Meanwhile, in the U.S., the UKG Workforce Activity Report shows that nearly two-thirds (63%) of manufacturers are struggling to fill crucial labor gaps. This blog explores the driving forces behind this workforce crisis, the risks of failing to retain skilled workers, and how connected worker technologies can help improve employee retention, safety, and shopfloor efficiency.
A Long-Standing and Evolving Talent Crisis
Manufacturers have been grappling with a talent shortage for years, but the issue is becoming increasingly complex due to several factors:
1. An Aging Workforce
A significant portion of the manufacturing workforce is nearing retirement, with too few younger workers entering the field to replace them. Data from the U.S. Bureau of Labor Statistics (2022) shows that the median age of manufacturing workers is 44.3 years—older than the national workforce average of 42.3 years. Additionally, 2023 Lightcast data indicates that over 51% of manufacturing roles are held by individuals aged 45 to 65+, intensifying the industry’s generational skills gap.
2. The Perception Problem
Manufacturing has long struggled with an image issue. Jobs in the sector are often viewed as low-skill, physically demanding, and outdated, discouraging younger generations from pursuing careers in the field. The tech industry’s growth, with its higher salaries and modern work environments, has further drawn talent away. Deloitte estimates that by 2030, the U.S. manufacturing sector could have 2.1 million unfilled jobs due to this ongoing perception challenge.
3. The Shift from Offshoring to Reshoring
For decades, manufacturing jobs were offshored to countries with lower labor costs. While this benefited businesses financially in the short term, it resulted in a loss of domestic skills. Now, as manufacturers reshore production, they are struggling to rebuild their workforce amid an industry-wide labor shortage.
4. The Digital Skills Gap
As automation, robotics, and data-driven processes become integral to manufacturing, the industry increasingly requires digital expertise. However, many current employees lack the necessary skills to operate and maintain these advanced systems. A 2022 IFS-IDC survey found that 48% of manufacturers cite a lack of digital skills as a major challenge preventing them from progressing with business transformation initiatives.
5. Evolving Workforce Expectations
The pandemic permanently reshaped workplace expectations. Many industries embraced remote and flexible work, setting new standards that are difficult to replicate in manufacturing environments. Younger employees, in particular, prioritize work-life balance, job satisfaction, and personal development opportunities. As digital natives, they also expect seamless integration of technology into their work.
As a result, manufacturing companies not only struggle to attract talent but also to retain it. Workers facing tough conditions, limited career development, or better salary offers elsewhere are more likely to leave, creating a high-churn environment.
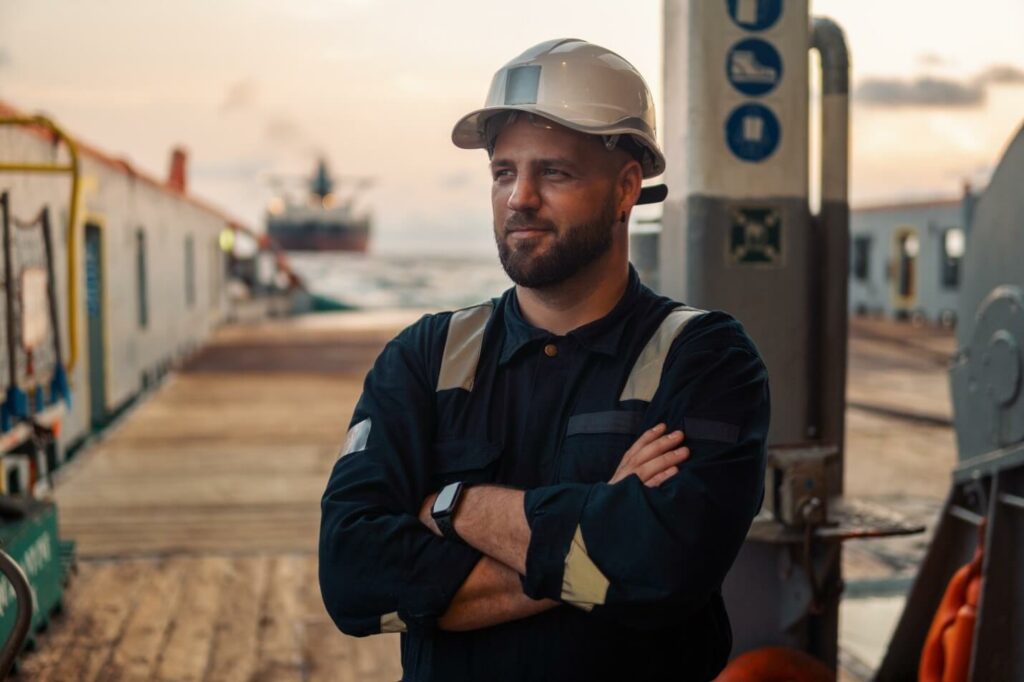
Recent Posts
The Impact of Workforce Attrition
Employee turnover is one of the biggest threats facing manufacturers today. In 2022, the sector’s overall turnover rate reached 39%, with an average attrition rate of 8.27% in the last quarter of the year. This high level of churn has serious consequences:
- Decreased Productivity: High employee turnover disrupts production schedules and workflows. New hires take time to reach full efficiency, affecting output quality and efficiency.
- Loss of Institutional Knowledge: Experienced workers possess invaluable expertise in equipment handling, quality control, and operational best practices. When they leave, companies risk losing critical knowledge that takes years to rebuild.
- Rising Hiring & Training Costs: Constantly recruiting and training new employees diverts resources from other business priorities, adding to operational costs.
- Increased Safety Risks: Experienced workers are typically more adept at following safety protocols and responding to emergencies. High turnover can lead to more workplace accidents, further impacting operational stability.
The Way Forward
Manufacturers must take proactive steps to address the talent crisis. In the second part of this blog series, we’ll explore strategies to enhance workforce retention, including training programs, flexible work arrangements, and digital transformation through connected shopfloor technology. By investing in employee experience and modernizing workplace practices, manufacturers can bridge the talent gap and secure a more resilient future.
About Xitricon
As a leading IFS Platinum Channel Partner Xitricon offers a transformative pathway for manufacturing enterprises aiming to seamlessly transition to IFS Cloud. With a commitment to precision and a robust suite of industry-specific solutions, Xitricon not only simplifies the migration process but also strategically enhances operational efficiency and long-term growth. Their proactive, collaborative approach ensures that every stage of your transformation is managed with exceptional care, setting a solid foundation for innovation and competitive advantage.
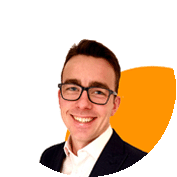
Ross Creed
Senior IFS Applications Consultant (FSM & PSO)